Falcon rockets use three configurations of their upper stage. How are they different?
It has long been known that SpaceX’s Falcon rockets use more than one type of upper stage depending on the needs of a given mission, but only now have we learned some more details. Falcon rockets actually use three different upper stages, which differ in how long they can last in orbit.
Back in 2019, SpaceX first tested a Falcon 9 with a second stage that was equipped with a grey stripe. Its purpose is to improve the thermal properties of the stage to maintain optimal temperatures in the propellant tanks. This is important for more demanding missions where the upper stage spends long periods of time in orbit, during which it needs to fire its engine several times, with several hours between ignitions. The grey stripe and other modifications to the stage prevent the fuel from freezing and also ensure the functionality of all systems during the long stay in orbit.
The stripe was first tested on the CRS-18 mission in July 2019, but we didn’t see the stripe in use again until June 2020 during the GPSIII-SV03 mission and then again in November 2022 when Falcon Heavy launched on the USSF-44 mission. All subsequent Falcon Heavies had the grey stripe, but we still didn’t know many details about all the differences between the stages with the grey stripe and those without it.
Another Falcon Heavy launched this week with the Jupiter-3 satellite and during the webcast, the SpaceX host provided a few details about the rocket’s upper stage. She explained:
Our second stages have three general configurations: standard, medium and long-coast. And we use different configurations depending on how long the second stage needs to operate after launch. A medium-coast kit, which is what we’re using today, provides better performance for some missions and includes an added battery loaf or power pack, a painted gray stripe on the outside of the fuel tank and other hardware to make sure that the fuel and stages systems operate as long as needed. While in space, that stripe of gray paint will absorb some heat from the Sun in order to keep the second stage fuel warm enough for a long flight today.
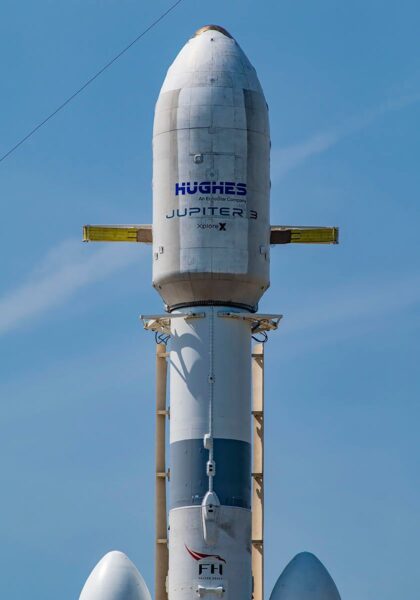
Falcon Heavy on pad 39A prior to the Jupiter-3 launch. The upper stage in the medium-coast configuration has the grey stripe. (Credit: SpaceX)
The standard upper stage is probably used for the least demanding missions, where the stage spends only an hour or two in orbit. For example, it’s used for Dragon and Starlink missions, where the payload is deployed just a few minutes after liftoff, or maybe after an hour. However, the stage needs to be operational for some time after that in order to perform a deorbit burn. That way it will disintegrate in the atmosphere and won’t become orbital debris that could cause problems for other objects in orbit in the future.
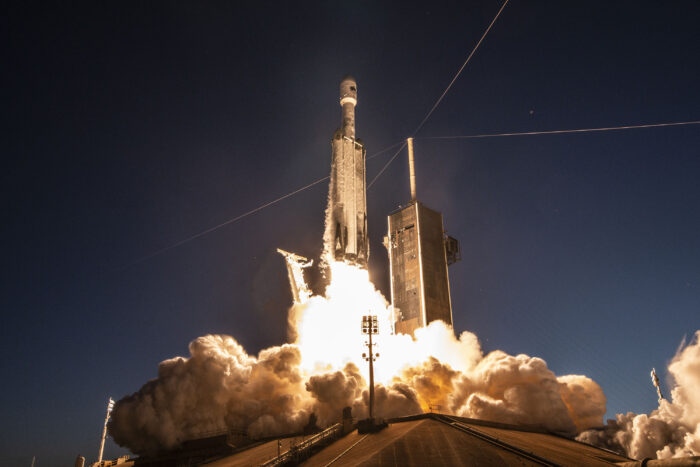
Falcon Heavy launching on the USSF-67 mission. This mission involved a very long coast for the upper stage. (Credit: SpaceX)
In the case of the Jupiter-3 mission, the payload deployment occurred approximately three and a half hours after liftoff, so it was a more challenging flight profile, requiring the “medium-coast” upper stage configuration with the grey stripe, additional batteries and other modifications. We don’t yet know exactly how the “long-coast” version of the stage differs, or whether it has ever been used, but I assume it has. For example, on this year’s USSF-67 mission, the Falcon Heavy upper stage reportedly had to spend over 6 hours in orbit, which probably required the version that can coast for the longest time.
Thank you! Is it known if there are also any differences with the engines? I saw at least one second stage with a different Merlin engine, way shorter than the engines I’m used to.
Yes, they use a Merlin Vacuum engine with a shorter nozzle on some missions that aren’t very demanding performance-wise. It’s a cost-saving measure.
Are we sure it’s a cost-saving measure instead of a G-force-reducing measure? For example if the payload were significantly lighter (or just more delicate), a shorter nozzle would mean less performance aka less G-forces, which would in theory reduce the G-forces experienced by the payload during 2nd stage burns.
Interesting theory. I think SpaceX themselves said the shorter nozzle reduces costs, so that part isn’t speculation, but maybe the reduced Gs are a nice bonus?
this means we have at least four (or even up to six) versions of the upper stage, depending on which engine is used.
So far the short-nozzle engine has only used with standard versions and I am not sure if it is available with the medium or long duration kits.